PLASMATRACK
Track cleaning solution
PlasmaTrack is a UK startup developing a plasma solution to disrupt the rail cleaning industry - removing the organic debris from rail tracks at speed and at low cost, ending years of misery from delayed and cancelled trains and reducing annual cleaning costs for rail networks.
"Network Rail is more than happy to continue to support the development of this innovative technology. The sensing technology in particular looks really interesting, because it has the potential to provide insight that the industry has been lacking on the development of contamination and consequent deterioration of rail conditions."
Daniel Booth
Seasons Delivery Specialist, (Wales)
Network Rail
The problem
Across Europe, what's known as leaves on the line is a £1.3Bn problem for the rail industry and the estimated societal cost in the UK alone is £350Mn. Organic debris from leaves creates a compacted layer on rail tracks reducing braking effectiveness resulting in slower and often cancelled services. Existing solutions to remove the slippery substance from rail tracks are costly, slow and has mixed results.
Using the UK as an example, water jet and chemical treatments currently use around 180 million litres of water over the Autumn period and current detection of slippy areas can take days to feed into the cleaning schedule outside of busy cities. In the meantime, timetables are adjusted so trains never run closer than nine miles apart, allowing for cautious braking.
The challenge
The sheer size of machinery involved, the speed trains need to move at and the explosive power of a stream of plasma made this project technically challenging and potentially very dangerous. But the end-game was worth fighting for and the team persisted year on year, despite multiple set-backs expected with a project of this size, both in the lab and out on the tracks.
Whilst R&D, concept design and testing on tracks in the lab could happen all year round, it was only possible to test the effectiveness of the Plasma module outside during Autumn months. Tracks needed to be free of scheduled trains, have significant organic matter compressed and permissions, equipment and rail safety personnel available all at the same time.
The breakthrough
There were key two elements to the solution that The Imagination Factory developed for PlasmaTrack - 24/7 detection of organic matter and high speed removal. Both can be harnessed independently but together are a game-changer.
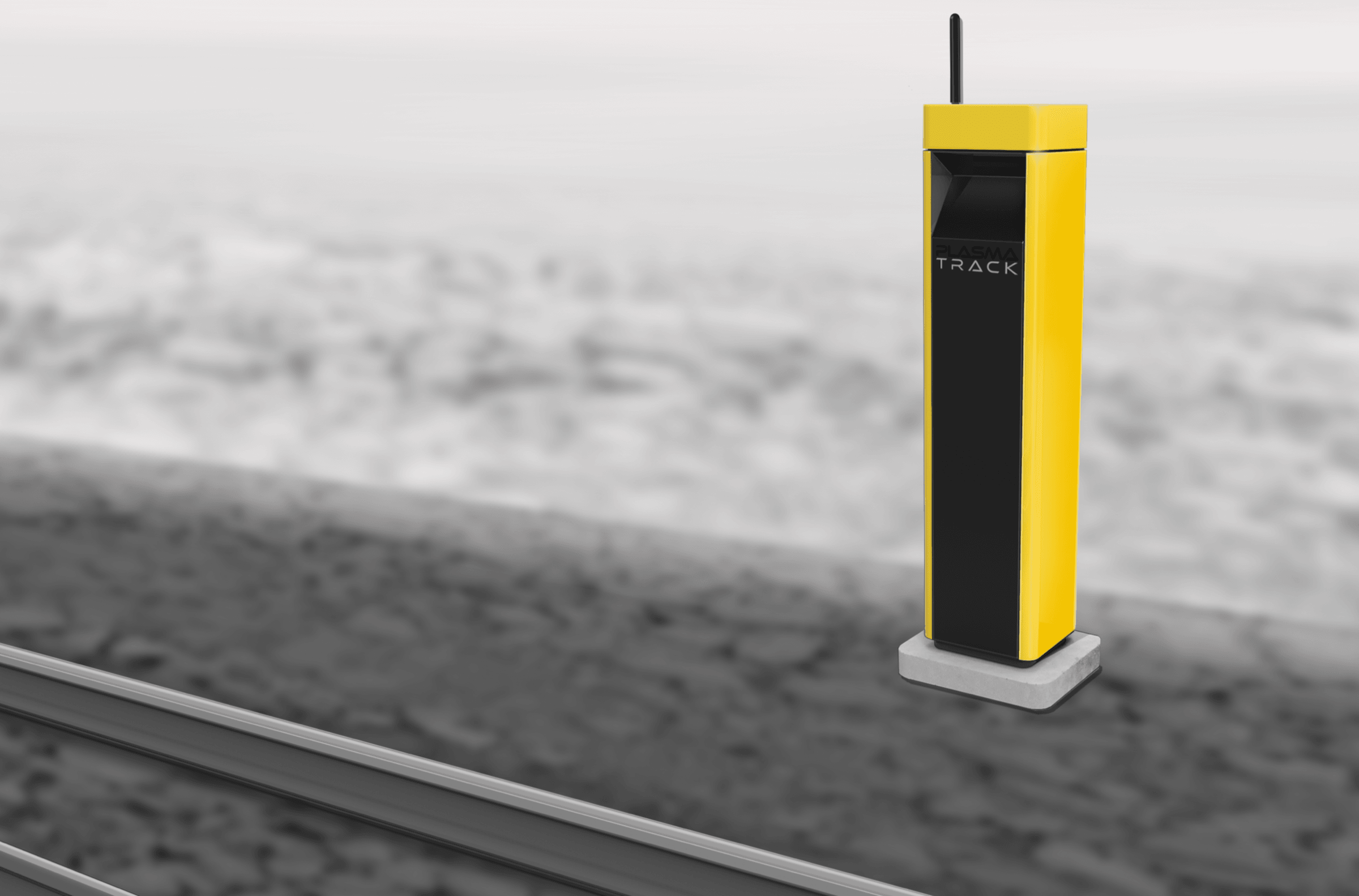
Detect
Aside from the huge reduction in water or sand that is currently transported around the network, purely for cleaning purposes, a track side or hand-held sensor will take the guess work out of cleaning schedules.
Designed by the team to complement the on-train PlasmaTrack modules, sensors provide reliable data on the rail condition 24/7.
Speed
Over four years, The Imagination Factory worked closely with specialists including British Steel, NPL and rail networks, to ensure PlasmaTrack removed leaf debris at speed, only where needed and without damaging rails in the process, giving drivers summer braking conditions all year round.
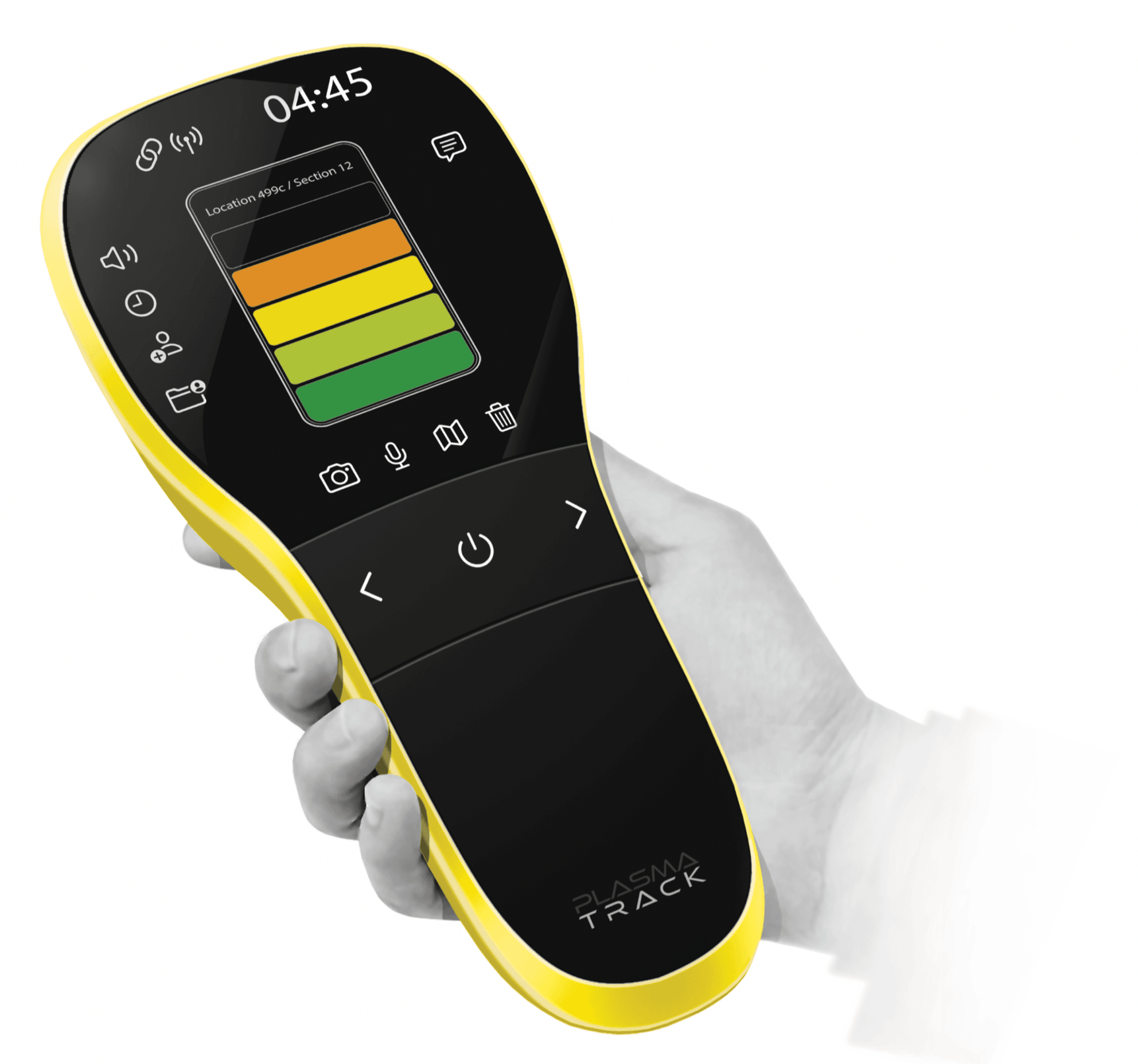
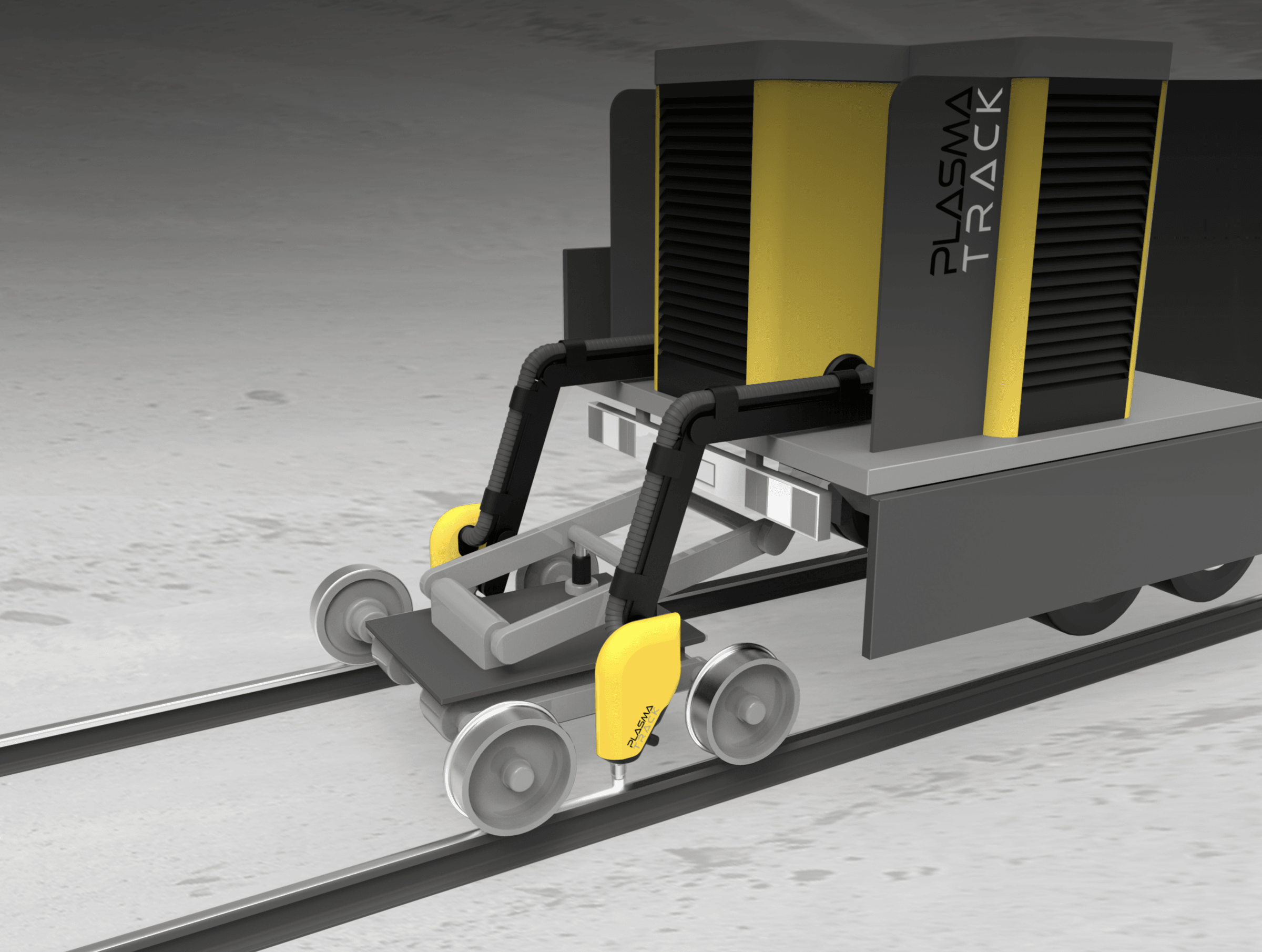
Our involvement
- Human-Centred Design research
- Concept development
- Sensor testing
- Ergonomic user testing
- Prototype construction
• Human-Centred Design research
• Concept development
• Scientific investigation
• Engineering design
• FEA + advanced engineering
• Analysis + simulation
• POP rig construction + testing
• Multiple prototype construction + testing
• Electronics design
• Design for manufacture
• Manufacturing + Production liaison
Work with us
If you have a design engineering project you'd like our help with, please get in touch with one of us at The Imagination Factory today.
We'd love to know more.